What Is Lean Manufacturing?
Lean manufacturing is often referred to as simply “Lean” is a systematic approach to optimizing operations and enhancing efficiency within a manufacturing environment. It mainly focuses on eliminating waste, increasing productivity, and continuously making changes in the processes to deliver high-quality products or services, while minimizing waste.
Lean principles have been widely adopted across industries and have proven effective in maximizing value for both businesses and customers.
The Core Principles of Lean Manufacturing
Value:
Lean manufacturing centers around delivering value to customers by focusing on their needs and preferences. It requires a deep understanding of customer requirements and expectations, allowing organizations to align their processes accordingly.Waste Reduction:
Waste, in the context of lean production system, refers to any activity or process that does not add value to the final product. Lean methodologies strive to identify and eliminate different forms of waste, such as overproduction, excessive inventory, waiting times, unnecessary transportation, defects, and unnecessary motion.Continuous Improvement:
A key aspect of lean production is the commitment to continuous improvement. This involves engaging employees at all levels to constantly seek ways to optimize processes, reduce waste, and enhance efficiency. Constant improvement fosters a culture of innovation, learning, and adaptability within the organization.Flow and Pull:
Lean manufacturing emphasize the concept of a smooth flow of work, with minimal interruptions or delays. By establishing a pull system, where production is based on actual customer demand rather than forecasted projections, organizations can avoid overproduction and excess inventory, leading to a more efficient and responsive operation.Respect for People:
Lean production recognizes that the employees are the foundation of any successful operations. It promotes a culture of respect, empowerment, and collaboration, encouraging employees to contribute their ideas, skills, and expertise to process improvement initiatives. By valuing and developing their workforce, organizations can create an environment that fosters innovation and drives overall success.
Benefits of Lean Manufacturing
Implementing lean manufacturing principles can yield significant benefits for businesses including:
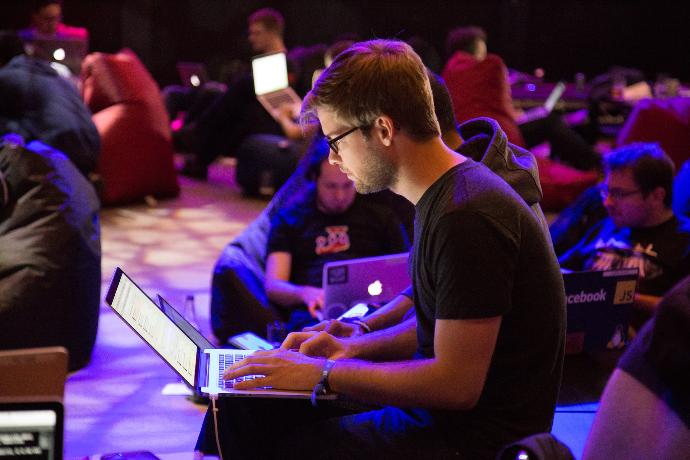
Improved Efficiency
Lean methodologies help identify and eliminate non-value-added activities, reducing waste and improving overall efficiency. By speeding up processes, organizations can optimize resources utilization and enhance productivity.
Enhanced Quality
Lean manufacturing focuses on defect prevention rather than detection. By continuously improving processes and implementing robust quality control measures, organizations can deliver products and services with higher quality standards, leading to increased customer satisfaction.
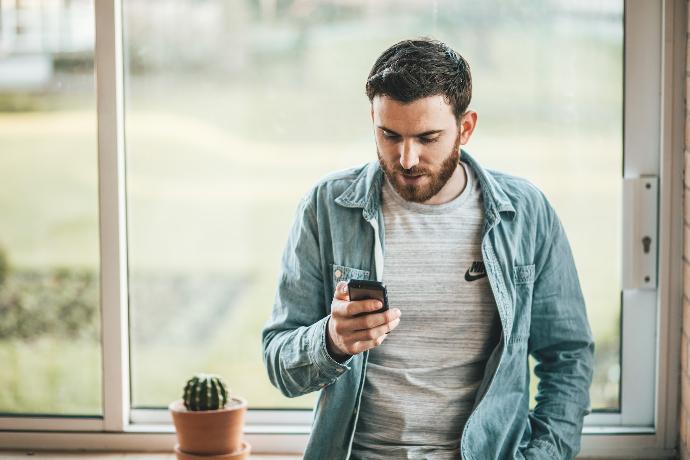
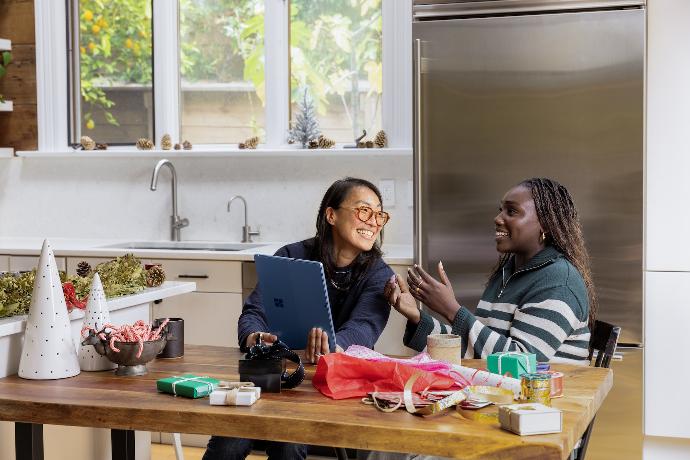
Reduced Cost
Through waste reduction and improved efficiency, lean manufacturing helps minimize costs associated with excess inventory, overproduction, defects, and other non-value-added activities. This enables organizations to achieve cost savings and improve their bottom line.
Faster Lead Times
Lean principles emphasize flow and pull, enabling organizations to respond more quickly to customer demands. By reducing cycle times and eliminating bottlenecks, businesses can achieve short lead times, resulting in improved customer responsiveness and market competitiveness.
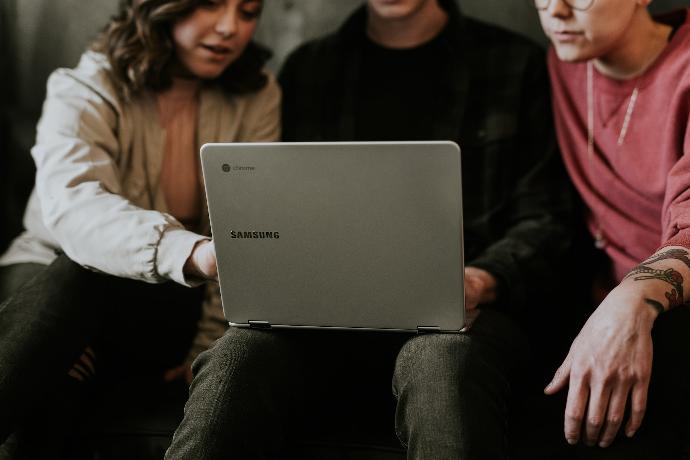
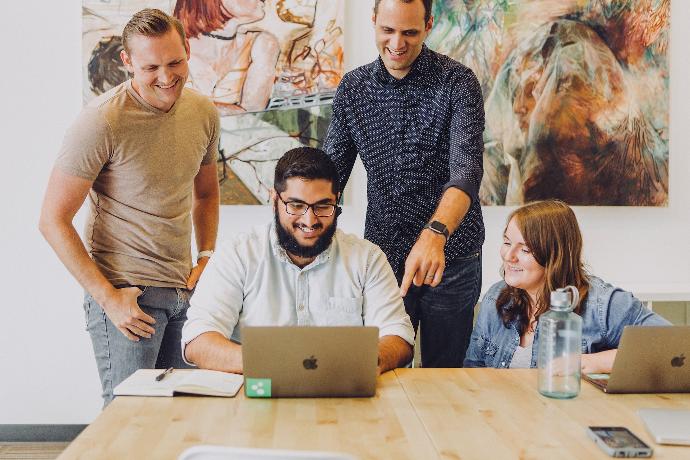
Employee Management
Lean manufacturing promotes a culture of empowerment and employee involvement. By valuing their contributions and providing opportunities for growth and development, businesses can foster a motivated and engaged workforce, leading to higher employee satisfaction and retention.
Companies that specialize in lean production provide a range of services aimed at optimizing and improving the efficiency of manufacturing processes. Here are some common types of services offered in this domain:
Lean Manufacturing Consulting
Lean manufacturing consultants work closely with companies to assess their existing manufacturing processes, identify areas of waste and inefficiency, and develop strategies to implement lean principles. They provide expert advice, guidance, and customized solutions to help organizations achieve operational excellence.
Process Analysis and Optimization
These services involve analyzing the entire manufacturing process, from raw materials to finished products, with the goal of identifying bottlenecks, inefficiencies, and non-value-added activities. Companies then develop and implement improvement plans to streamline operations, reduce waste, and improve overall productivity.
Value Stream Mapping (VSM)
Value stream mapping is a visual tool used to analyze and optimize the flow of materials and information throughout the manufacturing process. Companies offer VSM services to help identify areas of waste, excessive inventory, and process delays. Based on the analysis, they assist in designing future-state value streams and implementing changes to eliminate waste and improve overall efficiency.
Kaizan Events and Workshops
Kaizan is a methodology that focuses on making small, incremental changes in processes to achieve significant improvements over time. Companies provide Kaizan event facilitation and workshops to train employees in lean principles, problem-solving techniques, and empower them to actively participate in improving processes.
Lean Training and Education
Many companies offer training programs and workshops to educate employees at all levels on lean manufacturing tools, concepts, and techniques. This includes training on waste reduction, standardized work, 5S methodology, lean management, visual management, and other lean principles to create a culture of improvement within the organization.
Lean Six Sigma Integration
Lean Six Sigma combines lean manufacturing principles with Six Sigma methodologies for process improvement. Companies offer services to integrate these approaches, aiming to eliminate waste while reducing process variation and defects. They provide training, project management, and consulting to help organizations achieve the dual benefits of lean and Six Sigma.
Supply Chain Optimization
Lean manufacturing principles can be extended to optimize the entire supply chain, from sourcing raw materials to delivering finished products to customers. Companies provide services to evaluate and improve supply chain processes, including inventory management, supplier relationships, demand forecasting, and logistics optimization.
Lean Software and Technology Solutions
Some companies develop and offer software tools and technology solutions specifically designed to support lean production initiatives. These solutions may include production planning and scheduling software, real-time performance monitoring systems, visual management tools, and other digital solutions to streamline operations and improve visibility across the manufacturing floor.
Odoo, an open-source enterprise resource planning (ERP) system, aids in lean manufacturing by streamlining and optimizing various aspects of the production process. First, it centralizes and integrates data from different departments, enabling real-time visibility into inventory levels, work orders, and production schedules. This facilitates accurate demand forecasting and inventory management, reducing waste and improving efficiency.
Odoo's comprehensive reporting and analytics feature provide valuable insights into production performance, helping manufacturers identify bottlenecks, optimize processes, and continuously improve their operations to achieve lean manufacturing goals.
50,000+ companies run Odoo to grow their businesses.
Join us and make your company a better place.